White laminated coated wool felt rolls, do you know its history?
Initially, the production of wool-backed felt rolls for stair floor protection was mainly concentrated in industrially developed countries such as Japan, the United States, and Europe. Due to the early development of industrialization in Europe and the United States, the demand for surface protection of products was entered earlier than in Asia, and the surface scratches encountered during the transportation, handling, warehousing, and even display of products have been greatly improved. China began to involve protective films in the late 1990s, and at the beginning it was mainly adhesive films. Polyethylene polyester fiber self-adhesive felt developed later and was not involved until after 2000. It has reached its peak in recent years. With the development and demand of the industry, printed adhesive-backed wool felt has also emerged. Stair floor protection felts with company logos can be customized according to customer requirements. This not only improves the product grade but also promotes the company’s brand, which has been well received in the industry!
What are the characteristics and uses of white protective felt rolls with adhesive?
Painter paint felt rolls are mainly used in decoration, home textiles, industry, hospitals and other scenes. They are environmentally friendly, breathable, waterproof, anti-static, anti-bacterial, anti-pulling, anti-tearing, anti-moth and other functions. The temperature resistance can reach -30℃-+80℃. It can also be reused according to the different construction environments and the wear of the PE film backing wool felt, effectively saving construction costs.
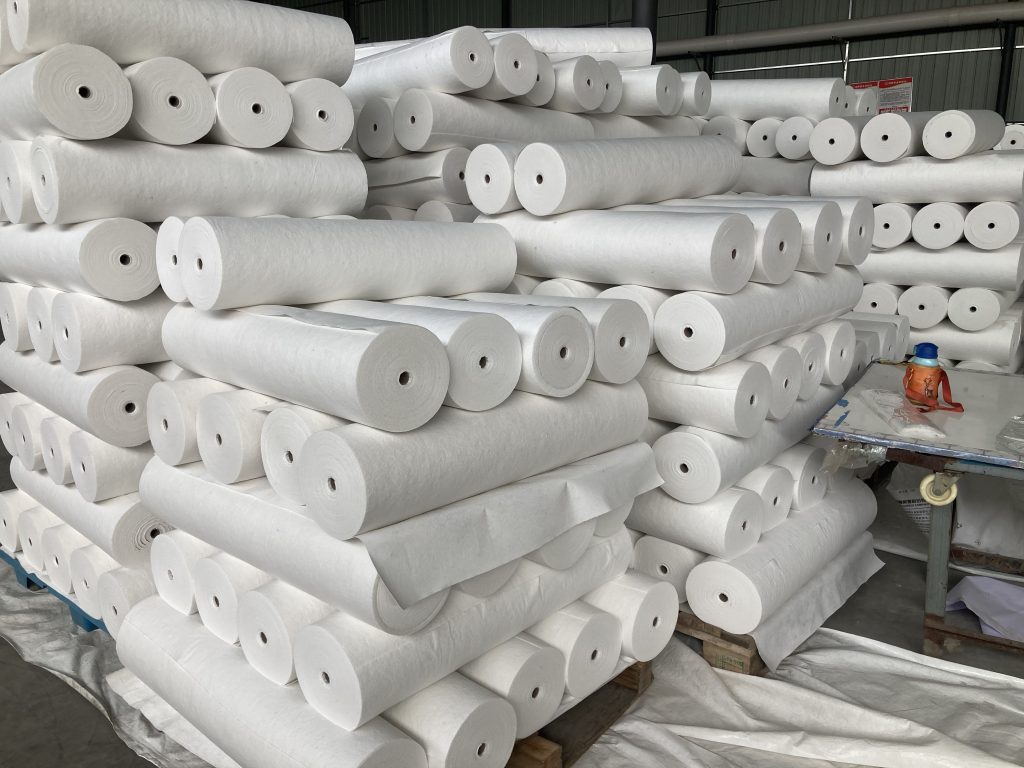
What are the requirements for the construction environment of white polyester wool felt rolls?
Most of Europe is dominated by flooring, which may be caused by the style. Many floors are made of matte materials. When laying floor protection felt, the dust on the ground needs to be cleaned and no water stains should be left. This is conducive to maintaining the best adhesion between the protective felt roll and the floor, so that the floor protection felt roll will not be separated from the floor from the beginning to the end of construction. Most tiles are made of glossy materials, which are easier to bond than floors when laid. The glue coating requirements are higher, and the glue ratio should be smaller than the former, so as to ensure that there will be no glue residue on the tiles after the construction is completed.
How much do you know about the technical parameters of white painters adhesive felt rolls?
Floor paint felt rolls are mainly composed of polyethylene film, polyester fiber, and water-based acrylic resin glue. They are made through lamination, spraying, drying and curing processes.
- The PE film should be made of high-pressure material, so that it can achieve both transverse and longitudinal tension and toughness. Ensure that the PE film will not be easily damaged during use. The thickness of commonly used polyethylene films is generally between 40g and 50g. Since the polyethylene film is very thin, polypropylene can be appropriately added according to customer requirements to increase the hardness of the product. In this way, the flatness of the product produced will be higher, the wear resistance of the product will be improved, and the overall appearance will also be improved.
- The selection of polyester fiber cotton is also very important. First of all, it must be a pure material product, so as to ensure the cleanliness of the product surface and no impurities will affect the beauty of the product. Now many factories choose recycled polyester fiber to reduce costs. Since the recycled material cannot clean the impurities inside, the products produced will have darker colored threads or black cotton, which directly lowers the grade of the product and fails to meet environmental protection standards. Polyester fiber cotton is usually divided into short-hair and long-hair. It is best to use short-hair cotton for making floor paint felt rolls, so as to avoid wool felt residues on the floor after the construction is completed. During use, the most common problem is that the diameter standards of the adhesive white felt rolls are different. Products of the same specifications and sizes will be large and small, which may be caused by the weight of polyester fiber. This problem can be roughly divided into two types: the first is that the equipment is old and cannot achieve accurate measurement of weight, and the thickness of the polyester fiber products produced is too different. The second is caused by the operator’s lack of experience or inexperience in controlling the equipment. For example (taking our factory as an example): the normal diameter of a 120g/㎡ 1m×50m white paint felt roll is 18cm. If the diameter can be controlled between 17cm and 19cm (with a positive and negative difference of 1cm), it is considered normal, because the tension of the rewinder determines the value trend of 1cm. If the diameter exceeds the normal value, it means that the weight and thickness of the polyester fiber are too different. The thickness of wool felt is usually between 80g-200g. If calculated by weight, a positive and negative difference of 6g is considered normal.
- Spraying water-based acrylic resin glue is the most important processing link, which directly determines the quality of the product. Water glue is a kind of glue that is odorless, non-toxic and highly environmentally friendly. It can be divided into low viscosity, medium-low viscosity, medium viscosity, medium-high viscosity and high viscosity according to the mesh number of the anilox roller. The corresponding viscosity can be selected according to customer requirements and construction environment. When spraying, it is necessary to add an appropriate amount of curing agent to ensure that the glue and polyester fiber cotton can be completely integrated when drying, so that there will be no glue residue on the floor after the construction is completed. Controlling the curing agent ratio is also a very important link. If the ratio is too small, the glue will fall off, and if the ratio is too large, it will directly affect the viscosity of the glue. If glue residue appears on the floor during construction, it is likely that the curing agent has not been added or the addition ratio is not well controlled. Finally, it should be noted that the glue with curing agent should be used up on the same day, because the curing agent reacts with the glue, especially in hot weather, and the product quality will be affected if it is used the next day.
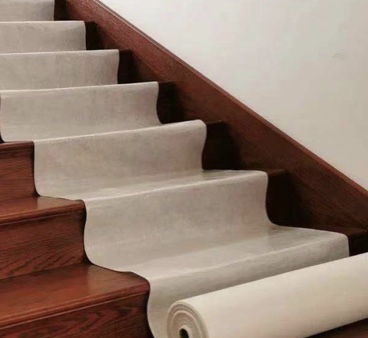